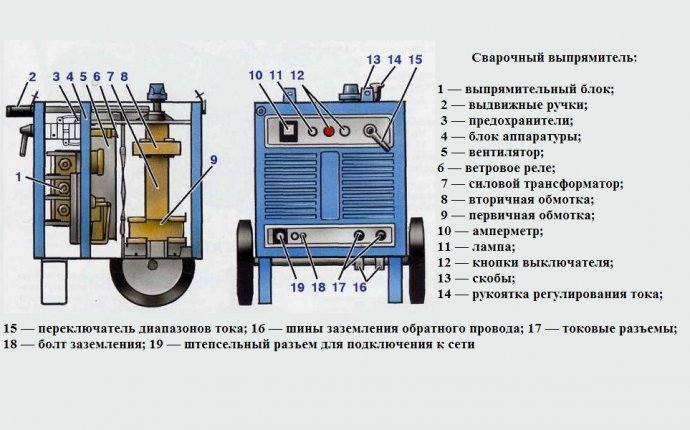
Welding Transformer Principle
Variable current welding is carried out by a low weld transformer. Welding transformer principle defined primarily Weld transformer principle to the idling speed of the converter capable of maintaining the working voltage of the burning arc. Usually, the idling range is 60 to 80 V. In the case of arc, the voltage falls to the working value, which depends on the specified weld current. The welding current is different and depends on welding regimes and the electrode used. The current is directly related to the weld speed, i.e. the quantity of the welded metal per unit of time. Therefore, a control device is used to adjust the current, most often a throttle. Call him double. Burning stability of welded arc depends to a great extent on the melting of the power supply. Pressure shocks at the port of the transformer contribute to breaking welded oath. The work of the regulator contributes to the smoothing of the rolls. Some welding transformers use a large-capacity condenser as a filter at the port of the transformer. Contemporary welding devices are designed for one-phase and three-phase power voltages 220 and 380 V, but the weld transformator principle does not depend on the number of phases or the amount of the power supply. The differences are the design and form of transformator magnetic wires and wet wires. Read also |